拋光、珩磨和磨削等傳統(tǒng)精整工藝不足以在航空航天、光學(xué)電子、醫(yī)療器械和核反應(yīng)堆等技術(shù)領(lǐng)域的設(shè)備制備工藝中實(shí)現(xiàn)較高要求的表面精整水平。MAF工藝則可以在管狀工件的內(nèi)外表面以及平面工件上實(shí)現(xiàn)較高的表面質(zhì)量;利用磁場中形成的磁性磨粒,MAF可以實(shí)現(xiàn)較高的工件表面和邊緣精加工。少量的磁性磨粒充當(dāng)切削工具,當(dāng)對(duì)工件施以相對(duì)運(yùn)動(dòng)時(shí)這些磨粒在工件表面受到壓縮并將待加工材料以切屑形式磨除掉。
Shinmura 等人在高溫高壓條件下將平均直徑5μm的氧化鋁和鐵粉混合,在真空燒結(jié)爐中1.5小時(shí),將其制備成150μm粒度大小的磁性磨粒,對(duì)SS41材質(zhì)的工件進(jìn)行破碎和修整加工,并研究MAF工藝的基本原理。實(shí)驗(yàn)結(jié)果表明工件表面精整質(zhì)量得到了約40%的改善。 Aizawa等人利用磁性輔助磨料研磨工藝對(duì)非鐵磁管狀工件進(jìn)行內(nèi)表面精整加工。實(shí)驗(yàn)所用工件為不銹鋼衛(wèi)浴管,磁性磨料為氧化鋁和鐵粉混合制備而成;表面精整改善約48%。實(shí)驗(yàn)還對(duì)MAF工藝中潤滑劑的使用量進(jìn)行了研究,發(fā)現(xiàn)潤滑劑最佳用量可以改善磨料在工件表面的接觸進(jìn)而實(shí)現(xiàn)較好的表面精整且精度較高。Khairy等人研究了MAF工藝在精整加工銀器鋼棒的粗糙表面和鋒利邊緣時(shí)的有效性和穩(wěn)定性。實(shí)驗(yàn)將氧化鋁和鐵粉混合,在1400℃下置于盛放有惰性介質(zhì)的爐中進(jìn)行壓制,時(shí)間1小時(shí);然后將其破碎成小顆粒并進(jìn)行粒度篩選。實(shí)驗(yàn)結(jié)果表明MAF工藝能夠改善表明精整約52%。表面光滑度、紋理結(jié)構(gòu)和表面層等都要比珩磨、拋光等利用固結(jié)在鐵水泥粗顆粒上的精細(xì)磨料產(chǎn)生的表面精整質(zhì)量要好。
Kaur A.等人利用氧化鋁做磨料成分、鐵粉做鐵磁成分制備出普通磁性粘結(jié)磨料,然后進(jìn)行MAF工藝試驗(yàn)。表面精整改善程度最大為36%。
以上文獻(xiàn)可知,MAF工藝參數(shù)如磁性磨粒量、工件旋轉(zhuǎn)速度、磨粒粒度、加工時(shí)間、工件間隙和磁通量密度會(huì)影響表面精整質(zhì)量和材料去除率。
2、磁性磨料的制備
試驗(yàn)將300目鐵粉(體積比80%)和300目氧化鋁磨料(體積比20%)進(jìn)行手動(dòng)混合,置于1100℃燒結(jié)爐中,燒結(jié)完畢將其破碎成小顆粒并進(jìn)行粒度篩分,如圖1所示。所用磨料粒度為120、180和220(106μm、75μm和53μm)。

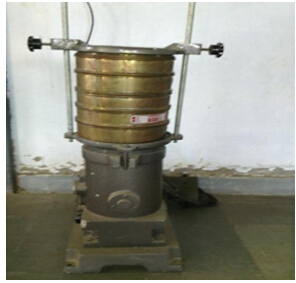
圖2為內(nèi)表面MAF工藝用實(shí)驗(yàn)裝置。磁性磨料堆放入管狀工件內(nèi),兩個(gè)永久磁鐵產(chǎn)生磁場。根據(jù)工件外直徑調(diào)整改變工件-磁鐵的工作間隙。
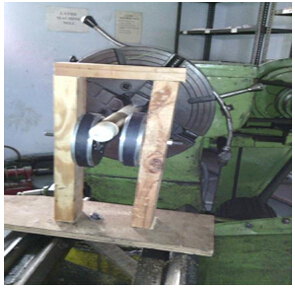
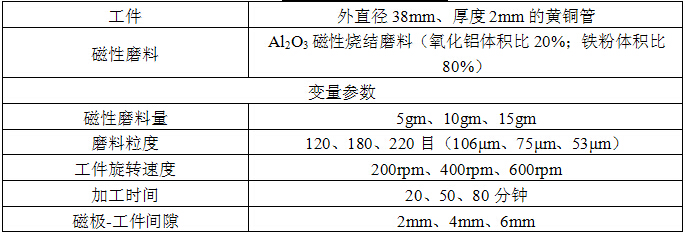
實(shí)驗(yàn)對(duì)工藝中的有效參數(shù)如磁性磨料量、工件旋轉(zhuǎn)速度、磨粒粒度、加工時(shí)間和工作間隙進(jìn)行改變并研究它們對(duì)表面粗糙度的影響。
圖3為磁性磨料量對(duì)平均表面粗糙度的平均值的影響。據(jù)圖可知,表面粗糙度隨磨料量增加而降低,說明磨料量增加可以改善表面精整質(zhì)量。表面粗糙度隨磨料粒度增大而降低。還可以看出表面粗糙度的降低隨著中間線的出現(xiàn)劃分出兩個(gè)基準(zhǔn),基準(zhǔn)1和基準(zhǔn)2;隨著工件-磁極的間隙增大,表面粗糙度數(shù)據(jù)從基準(zhǔn)1降低為基準(zhǔn)2進(jìn)而增大轉(zhuǎn)向基準(zhǔn)3。表面粗糙度隨工件旋轉(zhuǎn)速度的增大呈定量下降。隨著加工時(shí)間的延長,表面粗糙度由基準(zhǔn)1向基準(zhǔn)2定量下降,基準(zhǔn)2到基準(zhǔn)3的下降變化影響基本可以忽略。